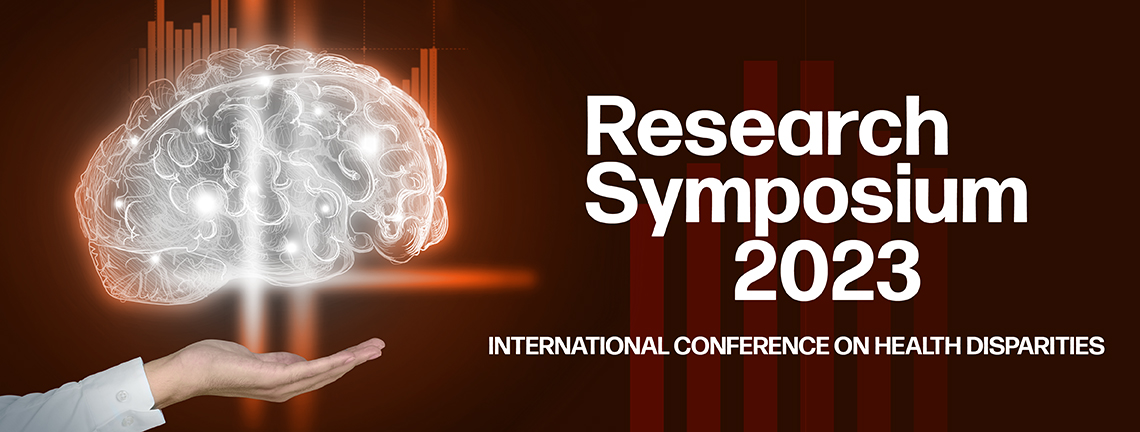
Posters
Presentation Type
Poster
Discipline Track
Biomedical ENGR/Technology/Computation
Abstract Type
Research/Clinical
Abstract
Background: Annually, there are over a million joint replacement procedures and more than 250,000 revision surgeries in the United States. The typical lifespan of a joint replacement ranges from 7 to 15 years, often curtailed by complications such as excessive implant wear leading to infections and joint dislocations. Given that most joint replacement recipients are between the ages of 50 and 70, the later part of their lives is often marred by repeated surgeries and discomfort. Presently, the predominant material used in joint replacements is medical-grade Ultra-High Molecular Weight Polyethylene (UHMWPE) with smooth surfaces. While these smooth surfaces are believed to minimize wear rate, studies have indicated that introducing micro-textures to these polyethylene components can further decrease wear, thereby enhancing the replacement's lifespan. This project aims to evaluate and optimize the use of a CNC machine to create surface micro-textures on UHMWPE discs. The study explores the impact of varying micro-drill bit sizes and spindle speeds on the micro-texturing process's precision, efficiency, and consistency. By understanding these influences, the project seeks to improve the production process for prosthetic components, ensuring high-quality and uniform textures that could enhance the durability and performance of such implants. In a future study, the tribological performance of different pattern microtextured UHMWPE discs will be evaluated by means of a Pin-on-Disk tribometer.
Methods: In the current project, discs with 1.125 inches in diameter and 0.25 inches in thickness were cut from a 12x12x0.25-inch UHMWPE sheet. A CNC 3-Axis machine was used to create the micro-textures on the UHMWPE discs. Three different surface micro-textures (dimple, cross hatch, and canal patterns) were selected for the experiment. These patterns are expected to generate different hydrodynamic responses under lubricated wear tests. The parameters of the micro-textures, such as dimple diameters, depth, and separation, were varied for the experiment. These terms refer to the size, depth, and the distance between the small depressions created on the surface of the UHMWPE discs. To create the different micro-textures, two different sizes of micro-drill bit diameters were used: 0.02” and 0.01”. The spindle speeds were set at 100 and 200 rpm. The diameters of the dimples and the distances between them were measured using a digital microscope.
Results: The experimental results showed that the micro-texturing process exhibited superior precision in creating the intended patterns on the UHMWPE discs. The diameters and depths of the micro-textures were consistent across all samples, as confirmed by measurements taken with the digital microscope. The dimple diameters and depths variance were less than 2% from the intended values, indicating high repeatability and consistency in the preparation process. A micro-drill bit size of 0.02” and a spindle speed of 200 rpm created the most desirable texture profiles for all three patterns.
Conclusions: In conclusion, the micro-texturing preparation process for UHMWPE discs proved to be highly efficient, precise, and consistent, offering promising implications for improving prosthetic implants' manufacturing process and performance. These positive results may lay the groundwork for more widespread adoption of micro-texturing techniques in the production of prosthetic components.
Academic/Professional Position
Faculty
Academic/Professional Position (Other)
Department of Mechanical Engineering
Recommended Citation
Ortega, Javier; Perez, J.; and Perez, N., "Enhancing the Tribological Performance of Prosthetic Implants: An Investigation of CNC Surface Micro-Texturing on UHMWPE" (2024). Research Symposium. 52.
https://scholarworks.utrgv.edu/somrs/2023/posters/52
Included in
Enhancing the Tribological Performance of Prosthetic Implants: An Investigation of CNC Surface Micro-Texturing on UHMWPE
Background: Annually, there are over a million joint replacement procedures and more than 250,000 revision surgeries in the United States. The typical lifespan of a joint replacement ranges from 7 to 15 years, often curtailed by complications such as excessive implant wear leading to infections and joint dislocations. Given that most joint replacement recipients are between the ages of 50 and 70, the later part of their lives is often marred by repeated surgeries and discomfort. Presently, the predominant material used in joint replacements is medical-grade Ultra-High Molecular Weight Polyethylene (UHMWPE) with smooth surfaces. While these smooth surfaces are believed to minimize wear rate, studies have indicated that introducing micro-textures to these polyethylene components can further decrease wear, thereby enhancing the replacement's lifespan. This project aims to evaluate and optimize the use of a CNC machine to create surface micro-textures on UHMWPE discs. The study explores the impact of varying micro-drill bit sizes and spindle speeds on the micro-texturing process's precision, efficiency, and consistency. By understanding these influences, the project seeks to improve the production process for prosthetic components, ensuring high-quality and uniform textures that could enhance the durability and performance of such implants. In a future study, the tribological performance of different pattern microtextured UHMWPE discs will be evaluated by means of a Pin-on-Disk tribometer.
Methods: In the current project, discs with 1.125 inches in diameter and 0.25 inches in thickness were cut from a 12x12x0.25-inch UHMWPE sheet. A CNC 3-Axis machine was used to create the micro-textures on the UHMWPE discs. Three different surface micro-textures (dimple, cross hatch, and canal patterns) were selected for the experiment. These patterns are expected to generate different hydrodynamic responses under lubricated wear tests. The parameters of the micro-textures, such as dimple diameters, depth, and separation, were varied for the experiment. These terms refer to the size, depth, and the distance between the small depressions created on the surface of the UHMWPE discs. To create the different micro-textures, two different sizes of micro-drill bit diameters were used: 0.02” and 0.01”. The spindle speeds were set at 100 and 200 rpm. The diameters of the dimples and the distances between them were measured using a digital microscope.
Results: The experimental results showed that the micro-texturing process exhibited superior precision in creating the intended patterns on the UHMWPE discs. The diameters and depths of the micro-textures were consistent across all samples, as confirmed by measurements taken with the digital microscope. The dimple diameters and depths variance were less than 2% from the intended values, indicating high repeatability and consistency in the preparation process. A micro-drill bit size of 0.02” and a spindle speed of 200 rpm created the most desirable texture profiles for all three patterns.
Conclusions: In conclusion, the micro-texturing preparation process for UHMWPE discs proved to be highly efficient, precise, and consistent, offering promising implications for improving prosthetic implants' manufacturing process and performance. These positive results may lay the groundwork for more widespread adoption of micro-texturing techniques in the production of prosthetic components.