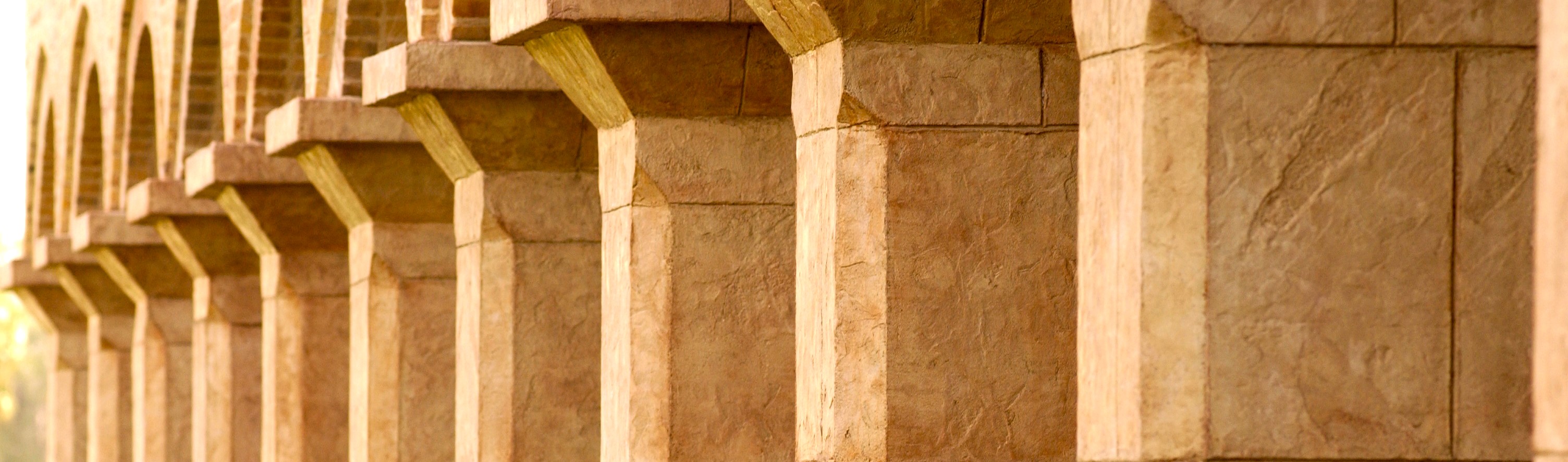
Mechanical Engineering Faculty Publications and Presentations
Document Type
Article
Publication Date
2-2024
Abstract
Magnetic Field Assisted Additive Manufacturing (MFAAM) enables 3D printing of magnetic materials of various shapes which exhibit a complex anisotropy energy surface containing contributions generated from different origins such as sample, particle, and agglomerate shape anisotropy, flow and field induced anisotropy, and particle crystal anisotropy. These novel magnet shapes require the need to measure the x, y, and z components of the magnetic dipole moment simultaneously to fully understand the magnetic reversal mechanism and unravel the complex magnetic anisotropy energy surface of 3D printed magnetic composites. This work aims to develop a triaxial vibrating sample magnetometer (VSM) by adding a z-coil set to a pre-existing biaxial VSM employing a modified Mallison coil set. The optimum size and location of the sensing coils were determined by modeling the sensitivity matrix of the z-coil set. The designed coil set was implemented using 3D printed spools, a manual coil winder, and gauge 38 copper wire. A 3D printed strontium ferrite nylon composite sample was used to estimate the sensitivity of the z-coils (50 mV/emu). The results herein are applicable for any VSM using a modified Mallison biaxial coil configuration allowing for a quick implementation on pre-existing systems.
Recommended Citation
Rodriguez, Leo, Arjun Sapkota, Jonathan Alvarado, Jitendra S. Tate, and Wilhelmus J. Geerts. "Computational modelling of a triaxial vibrating sample magnetometer." AIP Advances 14, no. 2 (2024). https://doi.org/10.1063/9.0000787
Creative Commons License
This work is licensed under a Creative Commons Attribution 4.0 International License.
Publication Title
AIP Advances
DOI
10.1063/9.0000787
Comments
Student publication. © 2024 Author(s). All article content, except where otherwise noted, is licensed under a Creative Commons Attribution (CC BY) license (http://creativecommons.org/licenses/by/4.0/).