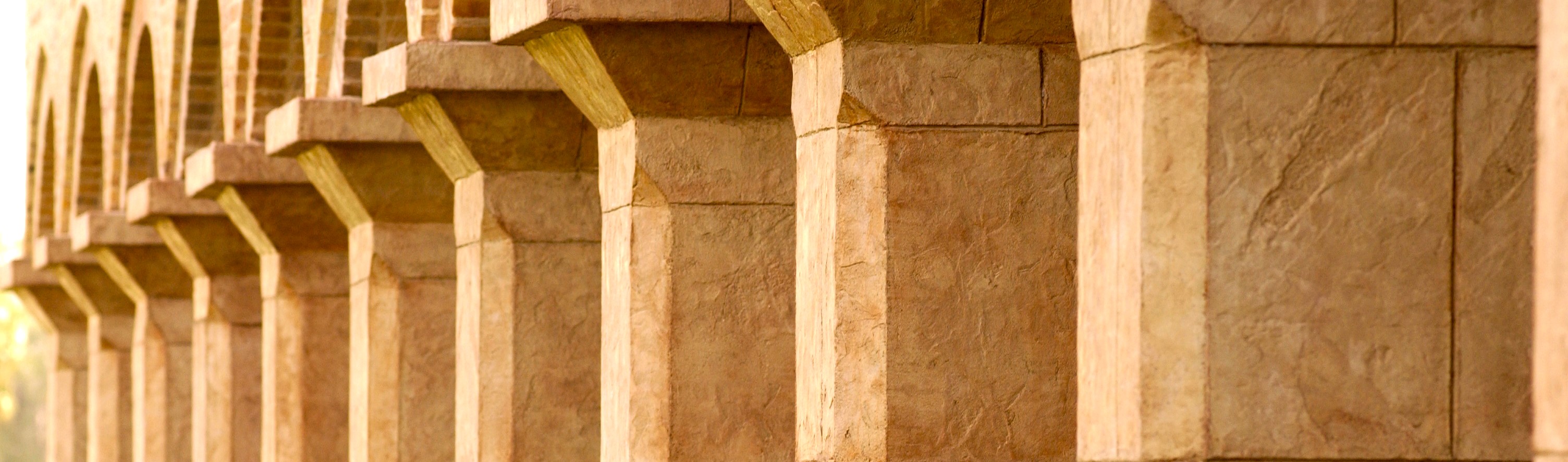
Mechanical Engineering Faculty Publications and Presentations
Document Type
Conference Proceeding
Publication Date
6-18-2018
Abstract
The railroad industry currently utilizes two wayside detection systems to monitor the health of freight railcar bearings in service: The Trackside Acoustic Detection System (TADS™) and the wayside Hot-Box Detector (HBD). TADS™ uses wayside microphones to detect and alert the conductor of high risk defects. Many defective bearings may never be detected by TADS™ due to the fact that a high risk defect is considered a spall which spans more than 90% of a bearing’s raceway, and there are less than 20 systems in operation throughout the United States and Canada. Much like the TADS™, the HBD is a device that sits on the side of the rail tracks and uses a non-contact infrared sensor to determine the temperature of the train bearings as they roll over the detector. The accuracy and reliability of the temperature readings from this wayside detection system have been concluded to be inconsistent when comparing several laboratory and field studies. The measured temperatures can be significantly different from the actual operating temperature of the bearings due to several factors such as the class of railroad bearing and its position on the axle relative to the position of the wayside detector. Over the last two decades, a number of severely defective bearings were not identified by several wayside detectors, some of which led to costly catastrophic derailments. In response, certain railroads have attempted to optimize the use of the temperature data acquired by the HBDs. However, this latter action has led to a significant increase in the number of non-verified bearings removed from service. In fact, about 40% of the bearings removed from service in the period from 2001 to 2007 were found to have no discernible defects. The removal of non-verified (defect-free) bearings has resulted in costly delays and inefficiencies.
Driven by the need for more dependable and efficient condition monitoring systems, the University Transportation Center for Railway Safety (UTCRS) research team at the University of Texas Rio Grande Valley (UTRGV) has been developing an advanced onboard condition monitoring system that can accurately and reliably detect the onset of bearing failure. The developed system currently utilizes temperature and vibration signatures to monitor the true condition of a bearing. This system has been validated through rigorous laboratory testing at UTRGV and field testing at the Transportation Technology Center, Inc. (TTCI) in Pueblo, CO. The work presented here provides concrete evidence that the use of vibration signatures of a bearing is a more effective method to assess the bearing condition than monitoring temperature alone. The prototype bearing condition monitoring system is capable of identifying a defective bearing with a defect size of less than 6.45 cm2 (1 in2) using the vibration signature, whereas, the temperature profile of that same bearing will indicate a healthy bearing that is operating normally.
Recommended Citation
Montalvo, J, Tarawneh, C, & Fuentes, AA. "Vibration-Based Defect Detection for Freight Railcar Tapered-Roller Bearings." Proceedings of the 2018 Joint Rail Conference. 2018 Joint Rail Conference. Pittsburgh, Pennsylvania, USA. April 18–20, 2018. V001T06A011. ASME. https://doi.org/10.1115/JRC2018-6210
Publication Title
Proceedings of the 2018 Joint Rail Conference
DOI
10.1115/JRC2018-6210
Comments
Copyright © 2018 by ASME