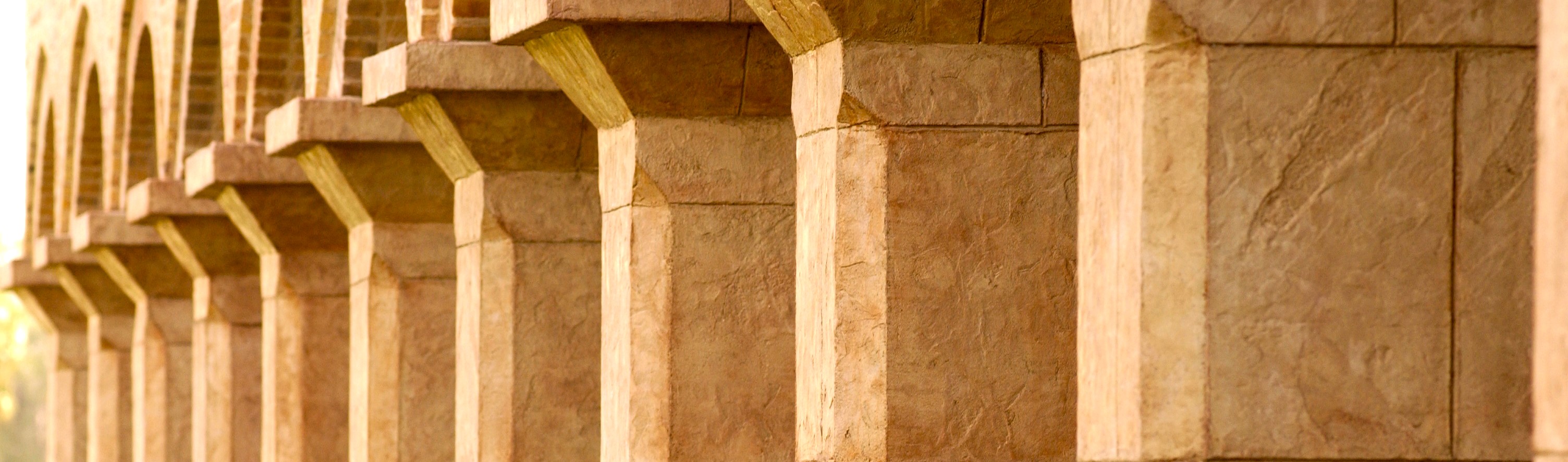
Mechanical Engineering Faculty Publications and Presentations
Document Type
Article
Publication Date
12-14-2019
Abstract
Thermoacoustics (TA) deals with the conversion of heat into sound and vice versa. The device that transfers energy from a low temperature reservoir to a high temperature one by utilizing acoustic work is called TA cooler (TAC). The main components of a typical TAC are a resonator, a porous regenerator (e.g. stack of parallel plates) and two heat exchangers. The thermoacoustic phenomenon takes place in the regenerator where a nonzero temperature gradient is imposed, and interacts with the sound wave. The low temperature at the cold end of TAC can be used to condense water from the humid air and also reduce the moisture. In the current study, the sound wave with high intensity was produced to drive a TAC to produce cooling power at a cold temperature around 18°C, using saturated water vapor as the working fluid. The drainage of condensate in the regenerator is the key to the system’s performance. This work is dedicated to investigate the effect from temperature gradient created in TAC on the condensation enhancement, by adopting three different designs of regenerators. 3D printer was used to design and fabricate different structures of regenerator, and then the systematic cooling capacity was tested and compared with different regenerators. This work can be extended to evaluate how the TA effect can be affected by the condensation if humid air is directly used as the working fluid. The potential application of this investigation can be an autonomous TAC system for water harvesting in arid areas.
Recommended Citation
Bekkulov, A., Luthen, A., and Xu, B. (December 14, 2019). "Experimental Study of Condensation in a Thermoacoustic Cooler With Various 3D-Printed Regenerators Using Water Vapor as the Working Fluid." ASME. J. Energy Resour. Technol. May 2020; 142(5): 050904. https://doi.org/10.1115/1.4045537
Creative Commons License
This work is licensed under a Creative Commons Attribution 4.0 International License.
Publication Title
Journal of Energy Resources Technology
DOI
10.1115/1.4045537
Comments
© 2019, ASME. Original published version available at https://doi.org/10.1115/1.4045537