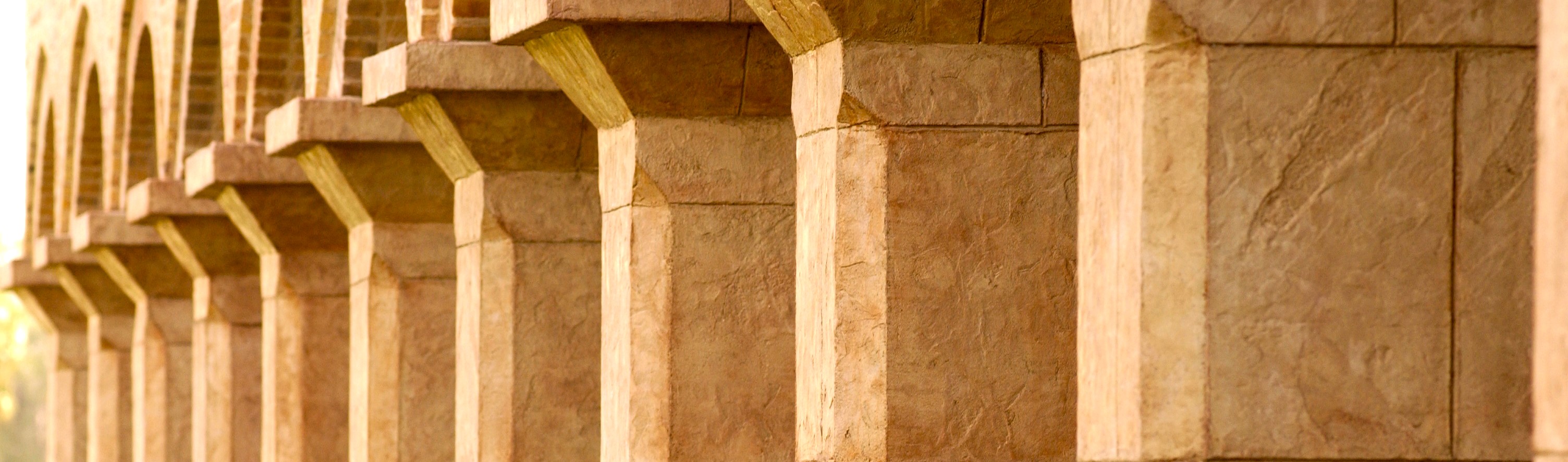
Manufacturing & Industrial Engineering Faculty Publications and Presentations
Document Type
Conference Proceeding
Publication Date
9-30-2022
Abstract
The powder bed fusion (PBF) process is widely adopted in many manufacturing industries because of its capability to 3D print complex parts with micro-scale precision. In PBF process, a thermal energy source is used to selectively fuse powder particles layer by layer to build a part. The build quality in the PBF process primarily depends on the thermal energy deposition and properties of the powder bed. Powder flowability, powder spreading, and packing fraction are key factors that determine the properties of a powder bed. Therefore, the study of these process parameters is essential to better understand the PBF process. In our study, we developed a two-dimensional powder bed model using the granular package of the LAMMPS molecular dynamics simulator. Cloud-based deposition was adopted for pouring powder particles on the powder bed. The spreading of particles over the substrate was mimicked like a powder bed system. The powder flowability in the proposed study was analyzed by varying the particle size distribution. The simulation results showed that a greater number of larger particles in a power sample results in an increase in the Angle of Repose (AOR) which ultimately affects the flowability. Two different kinds of recoater geometry were considered in this study: circular and rectangular blades. Simulation results showed that depending on the recoater shape there is a change in the packing fraction in the powder bed. Cross-sectional analysis of the power bed showed a significant presence of voids when a greater number of larger particles existed in the powder batch. The packing fraction of the powder bed was found to be a strong function of particle size distribution. These analyses help understand the influence of particle size and recoater shape on the powder bed properties. Findings from this study help to provide a guideline for choosing particle size distribution if the spherical particles are considered. While the present study focuses on the spherical powder particles, the proposed system can also be adapted to the study of powder bed with aspherical particles.
Recommended Citation
Akib, Yeasir Mohammad, et al. “A Numerical Study on the Powder Flowability, Spreadability, Packing Fraction in Powder Bed Additive Manufacturing.” Proceedings of the ASME 2022 17th International Manufacturing Science and Engineering Conference MSEC2022, ASME, 2022.
Publication Title
Proceedings of the ASME 2022 17th International Manufacturing Science and Engineering Conference
DOI
10.1115/MSEC2022-85323
Comments
© 2022 by ASME. Original published version available at https://doi.org/10.1115/MSEC2022-85323