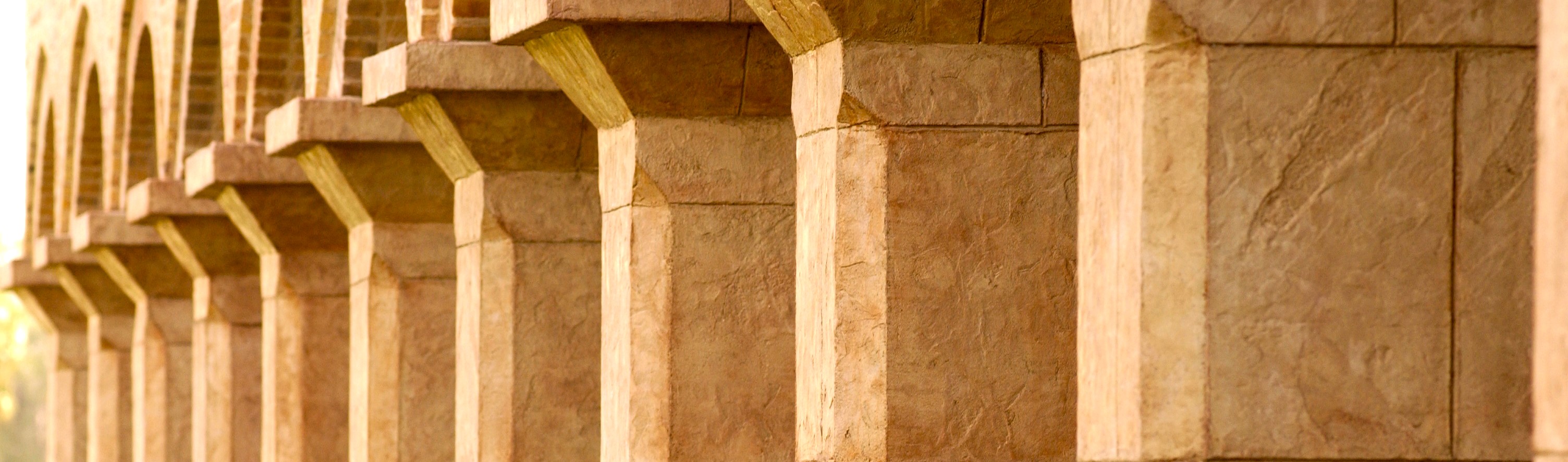
Manufacturing & Industrial Engineering Faculty Publications and Presentations
Document Type
Article
Publication Date
9-2022
Abstract
Carbon Fiber Reinforced Polymer (CFRP) composites have been widely used in aerospace, automotive, nuclear, and biomedical industries due to their high strength-to-weight ratio, corrosion resistance, durability, and excellent thermo-mechanical properties in non-oxidative atmospheres. Machining of CFRP composites has always been a challenge for manufacturers. In this research, a comparative study was performed between the optimal machining parameters of coated and uncoated carbide inserts obtained from the Multi-Objective Genetic Algorithm during turning of CFRP composites. It was found that coated carbide inserts provide lower tool wear and surface roughness, but higher cutting forces compared to those of uncoated carbide inserts during turning of CFRP composites. Taguchi Analysis was performed to investigate the effects of machining parameters (cutting speed, feed rate and depth of cut) on the output characteristics including cutting force, surface roughness and tool wear. The feed rate was found as the most significant machining parameter in turning of CFRP composites to minimize cutting force and surface roughness using both coated and uncoated carbide inserts. However, feed rate and cutting speed has been found as the most significant machining parameters for coated and uncoated carbide inserts respectively to minimize the tool wear. Regression Analysis has been performed to develop mathematical models for cutting force, surface roughness and tool wear as a function of cutting speed, feed rate and depth of cut. Higher R2 values and well fitted regression lines of normal probability plots in regression analysis indicate that the coefficients of mathematical models are statistically significant. The significance of this study is to emphasize the differences of performances between coated and uncoated carbide inserts during turning of CFRP composites in terms of cutting force, tool wear and surface roughness with the combination of different machining parameters (cutting speed, feed rate and tool wear) using data analysis tools such as Taguchi Analysis, Regression Analysis and Multi-Objective Optimization.
Recommended Citation
Rob, SM Abdur, and Anil K. Srivastava. "Turning of Carbon Fiber Reinforced Polymer (CFRP) Composites: Process Modeling and Optimization using Taguchi Analysis and Multi-Objective Genetic Algorithm." Manufacturing Letters 33 (2022): 29-40. https://doi.org/10.1016/j.mfglet.2022.07.012
Creative Commons License
This work is licensed under a Creative Commons Attribution-NonCommercial-No Derivative Works 4.0 International License.
Publication Title
Manufacturing Letters
DOI
10.1016/j.mfglet.2022.07.012
Comments
© 2022 Published by Elsevier Ltd on behalf of Society of Manufacturing Engineers (SME).