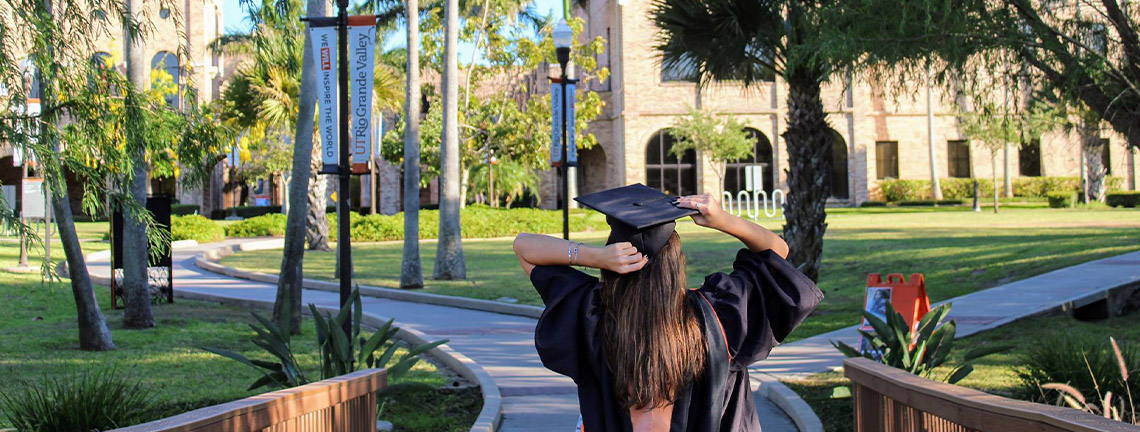
Theses and Dissertations
Date of Award
12-2020
Document Type
Thesis
Degree Name
Master of Science (MS)
Department
Manufacturing Engineering
First Advisor
Dr. Anil Srivastava
Second Advisor
Dr. Jianzhi Li
Third Advisor
Dr. Rajiv Nambiar
Abstract
Titanium alloys are extensively used in numerous industries like aerospace, automotive, military, etc., due to their exclusive characteristics. But machining these alloys has always been challenging for manufacturers. This research investigates the effect of radial depth of cut on cutting forces, tool life, surface roughness (Ra), and material removal rate (MRR) during face milling of Ti6Al4V alloy. It also aims to perform mono and multi-objective optimization of response characteristics to determine the optimal input parameters, namely cutting speed, feed rate, and radial depth of cut. Taguchi method and analysis of variance (ANOVA) have been used for mono-objective optimization, whereas Taguchi-based Grey relational analysis (GRA) and Genetic algorithm (GA) have been used for multi-objective optimization. Regression analysis has been performed for developing mathematical models to predict Ra, tool life, average cutting forces, and MRR. According to ANOVA analysis, the most significant parameter for tool life is cutting speed. For MRR and average cutting force (Avg. FY), the most influential parameter is the radial depth of cut. On the other hand, feed rate is the most significant parameter for Ra and average feed force (Avg. FX). The optimal combination of input parameters for tool life and Avg. FY is 50 m/min cutting speed, 0.2 mm/rev feed rate, and 7.5 mm radial depth of cut. However, the optimal parameters for Ra are 65 m/min cutting speed, 0.2 mm/rev feed rate, and 7.5 mm radial depth of cut. For Avg. FX, the optimal conditions are 57.5 m/min cutting speed, 0.2 mm/rev feed rate, and 7.5 mm radial depth of cut. Similarly, for MRR, the optimal parameters are 65 m/min cutting speed, 0.3 mm/rev feed rate, and 12.5 mm radial depth of cut. A validation experiment has been conducted at the optimal Ra parameters, which shows an improvement of 31.29% compared to the Ra measured at the initial condition. A minor error has been found while comparing the experimental data with the predicted values calculated from the mathematical models. GRA for multi-objective (3 objectives: tool life, Ra, and Avg. FY) optimization has improved 55.81% tool life, 6.12% Ra, and 23.98% Avg. FY. ANOVA analysis based on grey relational grade has demonstrated that radial depth of cut is the most significant parameter for multi-objective (three objectives) optimization during the face milling of Ti6Al4V. The results obtained from the GRA considering four output characteristics (tool life, Ra, Avg. FY, and MRR) are compared with GA optimization results for both roughing and finishing, and a negligible deviation has been observed.
Recommended Citation
Rahman, Al Mazedur, "Mono and Multi-Objective Optimization and Modeling of Machining Performance in Face Milling of Ti6Al4V Alloy" (2020). Theses and Dissertations. 747.
https://scholarworks.utrgv.edu/etd/747
Comments
Copyright 2020 Al Mazedur Rahman. All Rights Reserved.
https://go.openathens.net/redirector/utrgv.edu?url=https://www.proquest.com/dissertations-theses/mono-multi-objective-optimization-modeling/docview/2553783389/se-2?accountid=7119